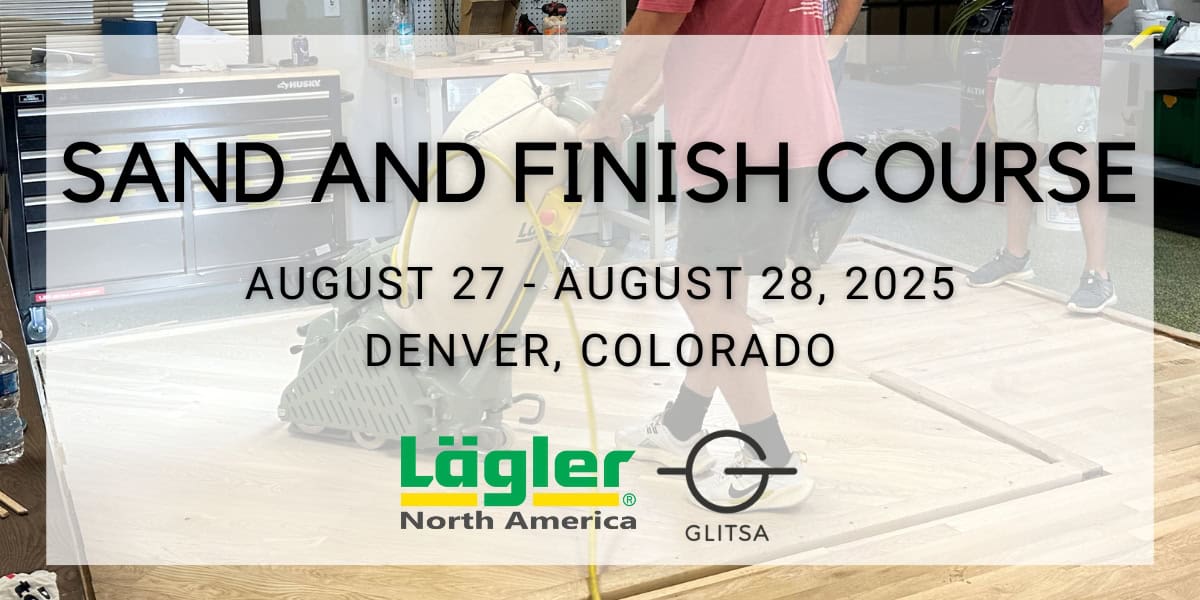
You are here:
Besides getting awesome Instagram shots on the job, of course, getting the floor flat is the most important part of sanding wood floors. But that’s harder to get just right if you don’t take a
Sanding wood floors is a science. Knowing that science is what sets you apart from DIY homeowners who want to save a buck and try their luck. In fact, when a lifestyle blogger reached out
This won’t surprise you, given Lägler is a German manufacturer, but the company focuses a lot on efficiency. Lägler cares about that in its production processes, and we care about helping sanding professionals be the
Have you ever compared a decades-old Lägler HUMMEL and a new one, and wondered what’s changed? We get it. At first glance, they look a lot alike. Two things: 1. Don’t change what ain’t broken
It’s story time. And while what you’re about to read might seem embellished or, parts of it, even flat-out fictional, what we say here is true. Every word. At the heart of this story is
HUMMEL owners, tell us: How easy is it to remove and replace your HUMMEL sanding drum? Yeah, easy-easy. DIY in the shop, at your trailer, on the jobsite floor, right? No need to waste time
There are a lot of parts to care about with a “big machine” like Lägler’s HUMMEL. But even if you keep it purring, clean and rolling smoothly, it won’t do you any good if you
This ain’t Vegas. What happens at the Lägler factory in Germany does not stay in the Lägler factory in Germany. It gets shipped near and far to floor guys in 142 countries. Take the HUMMEL.
How to Level the Wheels of the Lägler HUMMEL® OK, so you’re on your way into the house, carrying your HUMMEL. It gets dropped. It takes a lot to throw out of whack the wheel
We’re doing what people do at the end of one year, beginning of another. We look back at what we did well and what we can improve. We always want to keep doing better. That
Lägler North America, a division of Palo Duro Hardwoods, is the North American distributor of machines and parts manufactured by Eugen Lägler GmbH in Germany. We are North America’s machine repair center, and offer Lägler’s one-day Premium Sanding Technology (PST®) certification course.
Copyright © 2020 Lägler North America. All Rights Reserved.