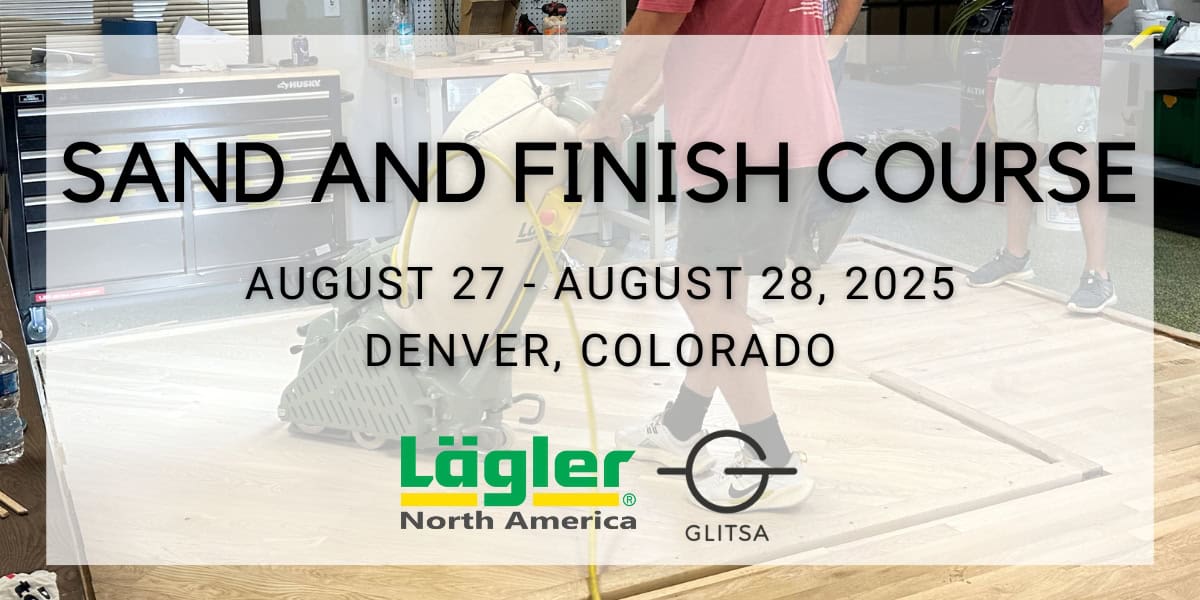
You are here:
Most abrasives are produced for other industries or for stationary belt sanding machines. These machines are mainly used to sand raw wood at a set speed, RPM and pressure. Those abrasives are then converted to
The last thing you want with a floor you’ve sanded and finished is to have sanding marks pop like neon signs in the night. If you can spot sanding marks while standing at full height
The past several months we’ve laid out how-to tips for using the big machine, edger, multi-disc sander and buffer. It’s a series of blog posts at your fingertips, but it’s also based on an industry-leading
We’ve been rolling through Lägler’s “Sanding of Wooden Floors” manual bit by bit. We’ve talked about how to pull the best work out of your crew and your machines using the big machine, edger and
Those who don’t know call the Lägler TRIO a buffer. Only those who don’t know. The way to feel what’s what is to get your hands on the TRIO and do some work – and
Guest Post by Brett Miller, NWFA VP of Education & Certification For those of you who think you don’t have time for training, think again. Certainly, there is no better feeling than being “too busy”
It seems to be something like an open secret that the Lägler FLIP® is engineered for versatility. The information is out there, in Lägler’s “Sanding of Wooden Floors” manual and in some pieces already on
A lot of floor sanding pros probably are confident in their “how to sand with a big machine” knowledge. Many of you should be. Yet here we are talking about it, so hang with us
Besides getting awesome Instagram shots on the job, of course, getting the floor flat is the most important part of sanding wood floors. But that’s harder to get just right if you don’t take a
Sanding wood floors is a science. Knowing that science is what sets you apart from DIY homeowners who want to save a buck and try their luck. In fact, when a lifestyle blogger reached out
Lägler North America, a division of Palo Duro Hardwoods, is the North American distributor of machines and parts manufactured by Eugen Lägler GmbH in Germany. We are North America’s machine repair center, and offer Lägler’s one-day Premium Sanding Technology (PST®) certification course.
Copyright © 2020 Lägler North America. All Rights Reserved.