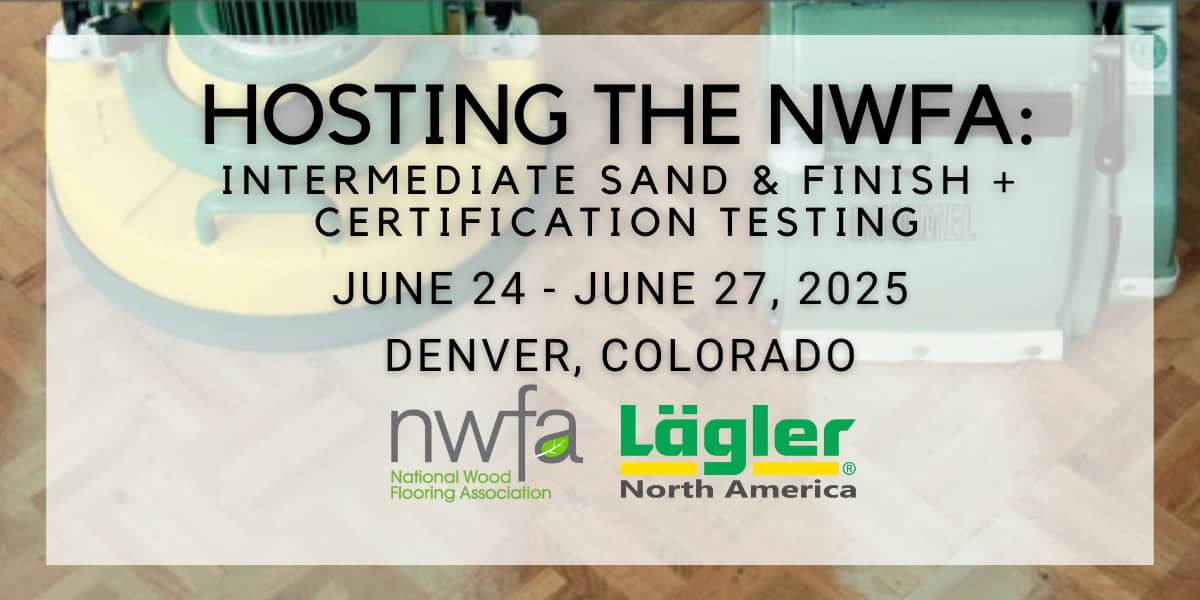
You are here:
Have you noticed your Lägler FLIP® acting a bit different lately? Maybe you’re having a tough time starting it or the working speed has decreased. Maybe it feels like it isn’t running as smoothly as
We’ve been rolling through Lägler’s “Sanding of Wooden Floors” manual bit by bit. We’ve talked about how to pull the best work out of your crew and your machines using the big machine, edger and
Those who don’t know call the Lägler TRIO a buffer. Only those who don’t know. The way to feel what’s what is to get your hands on the TRIO and do some work – and
There are two approaches to floor sanding: guesswork and science. Guesswork creates variables and challenges in sanding jobs that aren’t there. It causes the professional to change his or her approach from job to job,
This won’t surprise you, given Lägler is a German manufacturer, but the company focuses a lot on efficiency. Lägler cares about that in its production processes, and we care about helping sanding professionals be the
Have you heard of “hidden champions”? We recently heard this tag, what it means, and who it’s talking about. And started thinking about all the amazing champions in wood flooring. Pros who knock out beautiful
HUMMEL owners, tell us: How easy is it to remove and replace your HUMMEL sanding drum? Yeah, easy-easy. DIY in the shop, at your trailer, on the jobsite floor, right? No need to waste time
There are a lot of parts to care about with a “big machine” like Lägler’s HUMMEL. But even if you keep it purring, clean and rolling smoothly, it won’t do you any good if you
How to Mount the Lägler TRIO V-Belt In our previous blog post, we gave step-by-step instructions for removing the Lägler TRIO V-belt. Here are the steps for putting a new V-belt on the TRIO. First,
How to Remove the Lägler TRIO V-Belt Our how-to blog posts like this one are all about helping you to solve your maintenance questions, especially when you’ve got a tight schedule and need to keep
Lägler North America, a division of Palo Duro Hardwoods, is the North American distributor of machines and parts manufactured by Eugen Lägler GmbH in Germany. We are North America’s machine repair center, and offer Lägler’s one-day Premium Sanding Technology (PST®) certification course.
Copyright © 2020 Lägler North America. All Rights Reserved.