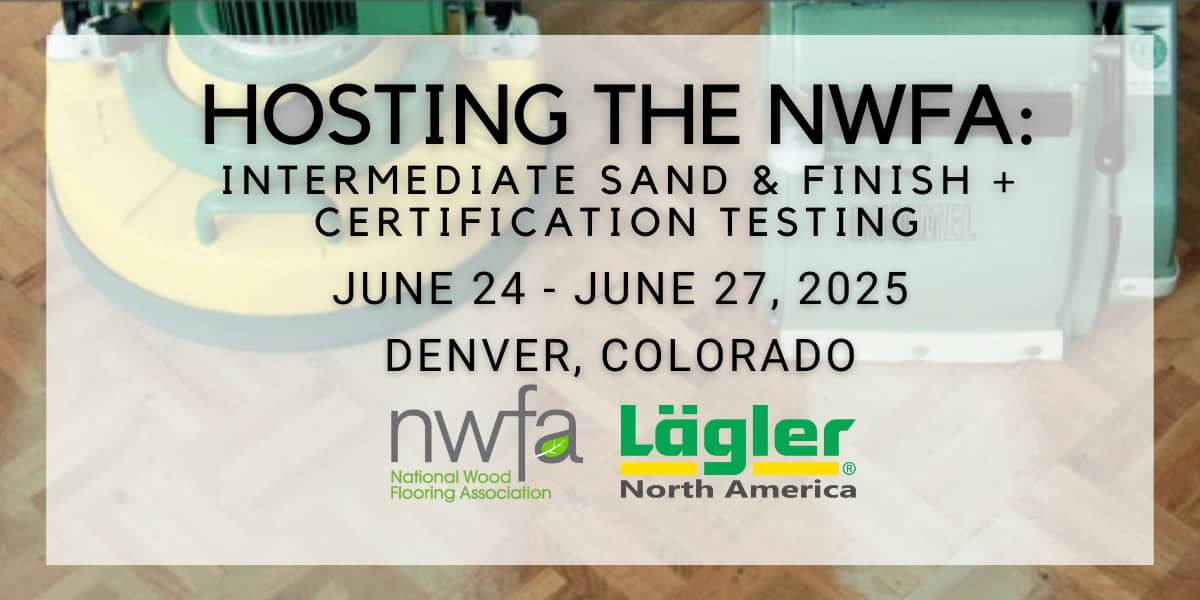
You are here:
Most abrasives are produced for other industries or for stationary belt sanding machines. These machines are mainly used to sand raw wood at a set speed, RPM and pressure. Those abrasives are then converted to
A lot of floor sanding pros probably are confident in their “how to sand with a big machine” knowledge. Many of you should be. Yet here we are talking about it, so hang with us
There are two approaches to floor sanding: guesswork and science. Guesswork creates variables and challenges in sanding jobs that aren’t there. It causes the professional to change his or her approach from job to job,
By Karl Lägler A goal for every contractor’s business should be to minimize effort and time on-site while maximizing quality results and profits. Wood floor sanding is hard work, but that doesn’t mean it can’t
Lägler engineers took on a special “Coke vs. Pepsi” kind of project in 2015. They spent more than eight months testing to see if the TRIO really held its own against competitors’ multi-disc attachments, and
Flexibility of tools on the job stands out. And the Lägler FLIP, with its corner attachment, can be one of the difference-makers on the job site. If you use a FLIP, you know the short
Have you noticed the six arrows on the bottom of a Lägler TRIO sanding disc? We point them out during our Premium Sanding Technology training (PST® certification). A lot of times, the guys hadn’t noticed
Lägler North America, a division of Palo Duro Hardwoods, is the North American distributor of machines and parts manufactured by Eugen Lägler GmbH in Germany. We are North America’s machine repair center, and offer Lägler’s one-day Premium Sanding Technology (PST®) certification course.
Copyright © 2020 Lägler North America. All Rights Reserved.